Towards the end of my undergraduate program, a group of students and I took part in a business/engineering crossover course. The final goal of the course was to prepare a compelling business plan to a group of business professionals who volunteered their time to act as judges in the final presentations for our course, and awarding the Ken Spencer award to the finalists. My team pulled off third place plus some extra cash for tuition and pizza.
We ended up deciding on proposing a new type of hearing aid for our final project. While it was not at all required for the course, I decided to actually build the device to give more weight to our business case, with initial R&D completed and a working prototype being available for the demo.
First, I wired up a microphone and speaker circuit with a Microchip dsPIC chip.
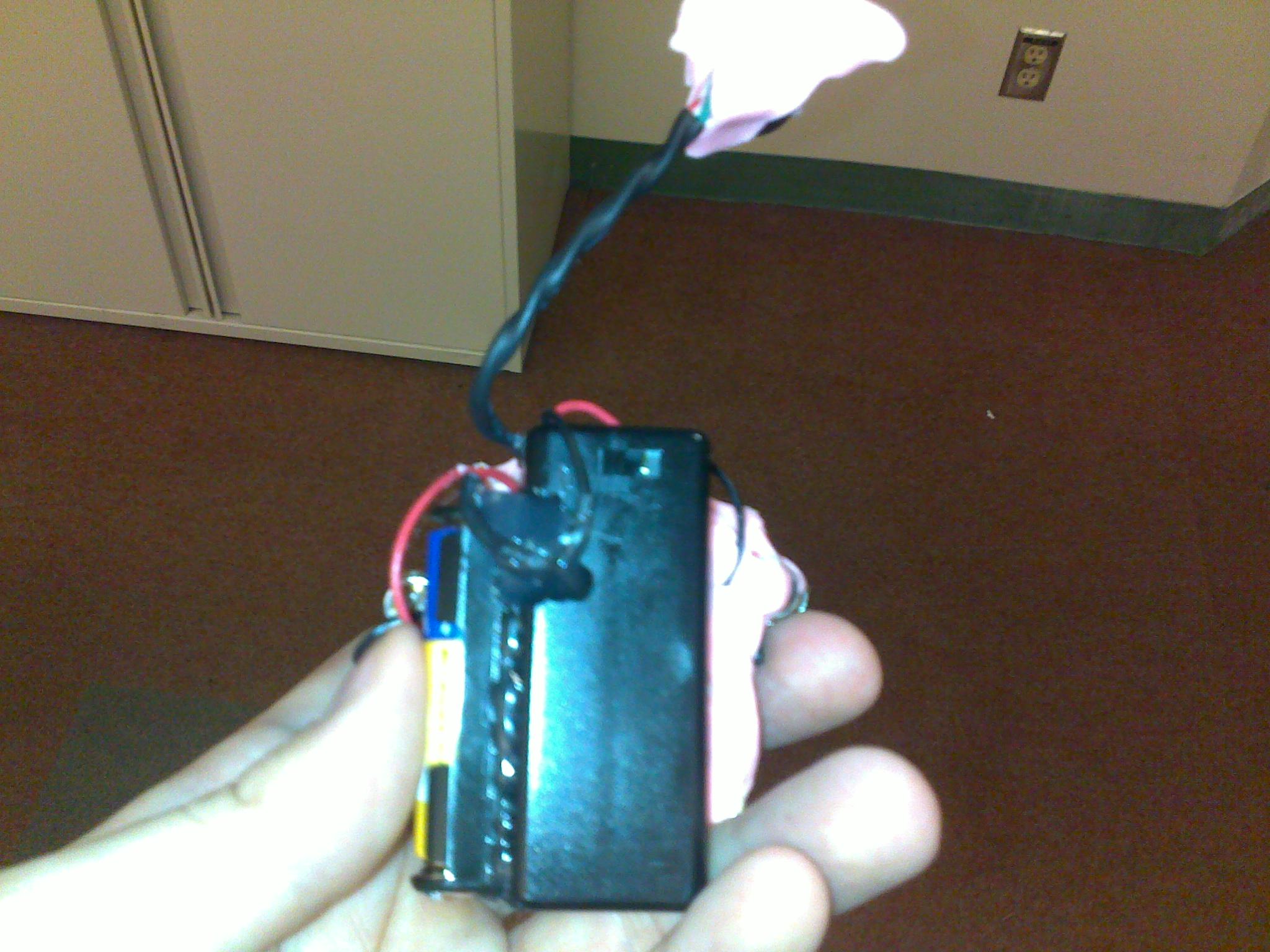
Initial AcousticAid prototype.
After getting the initial circuit working, I designing a linear acoustic echo cancellation algorithm and a digital filtering routine that ran in real time. I then managed to get a hold of audiologists’ putty to create a custom fitting mould for my ear.
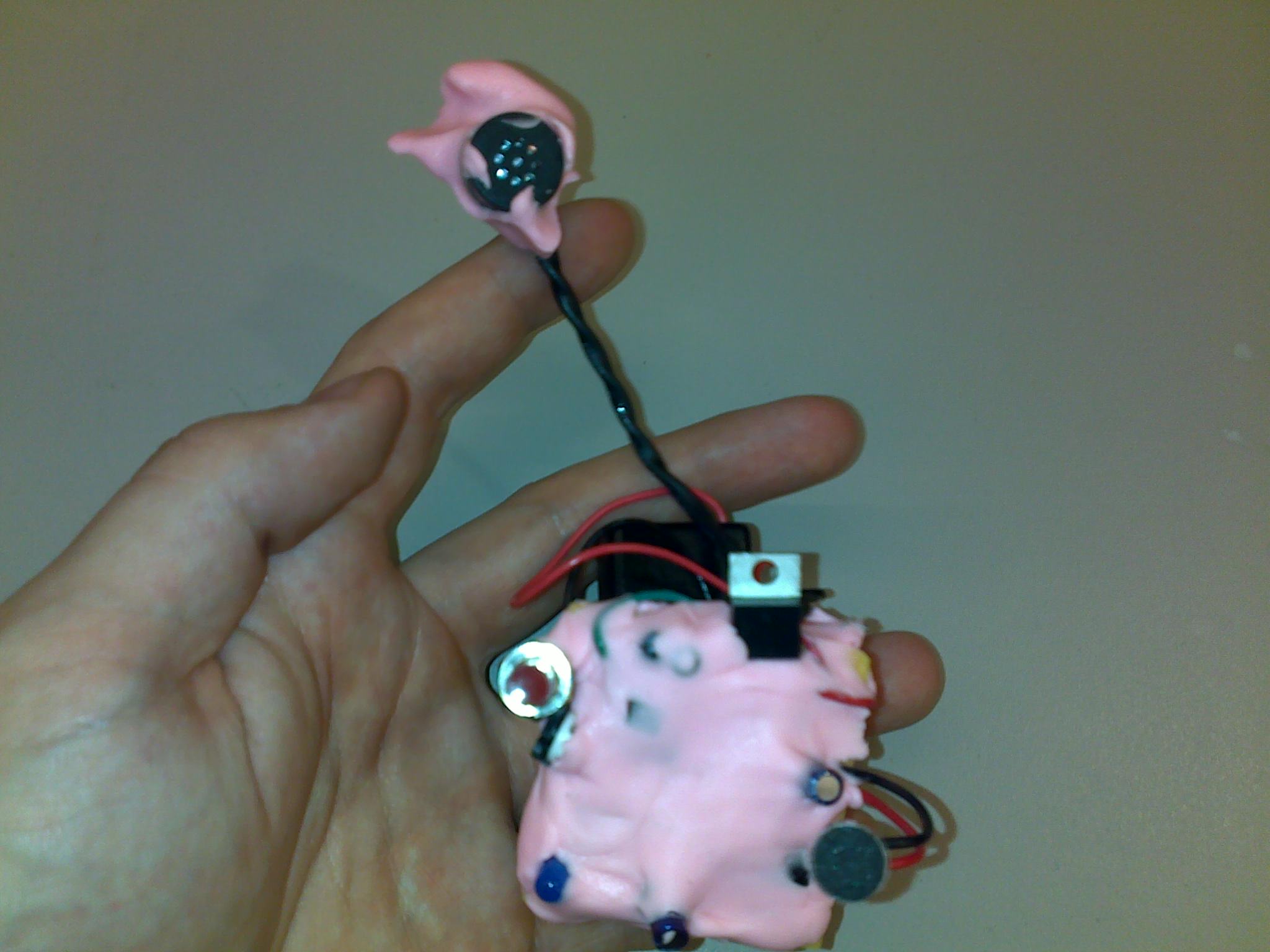
Device with custom mould applied.
So far so good. It works, but could use a bit more in term of aesthetics. Since I had a PCB etching tank I had built myself, I figured we could move to smaller surface mount components if we made our own PCB.
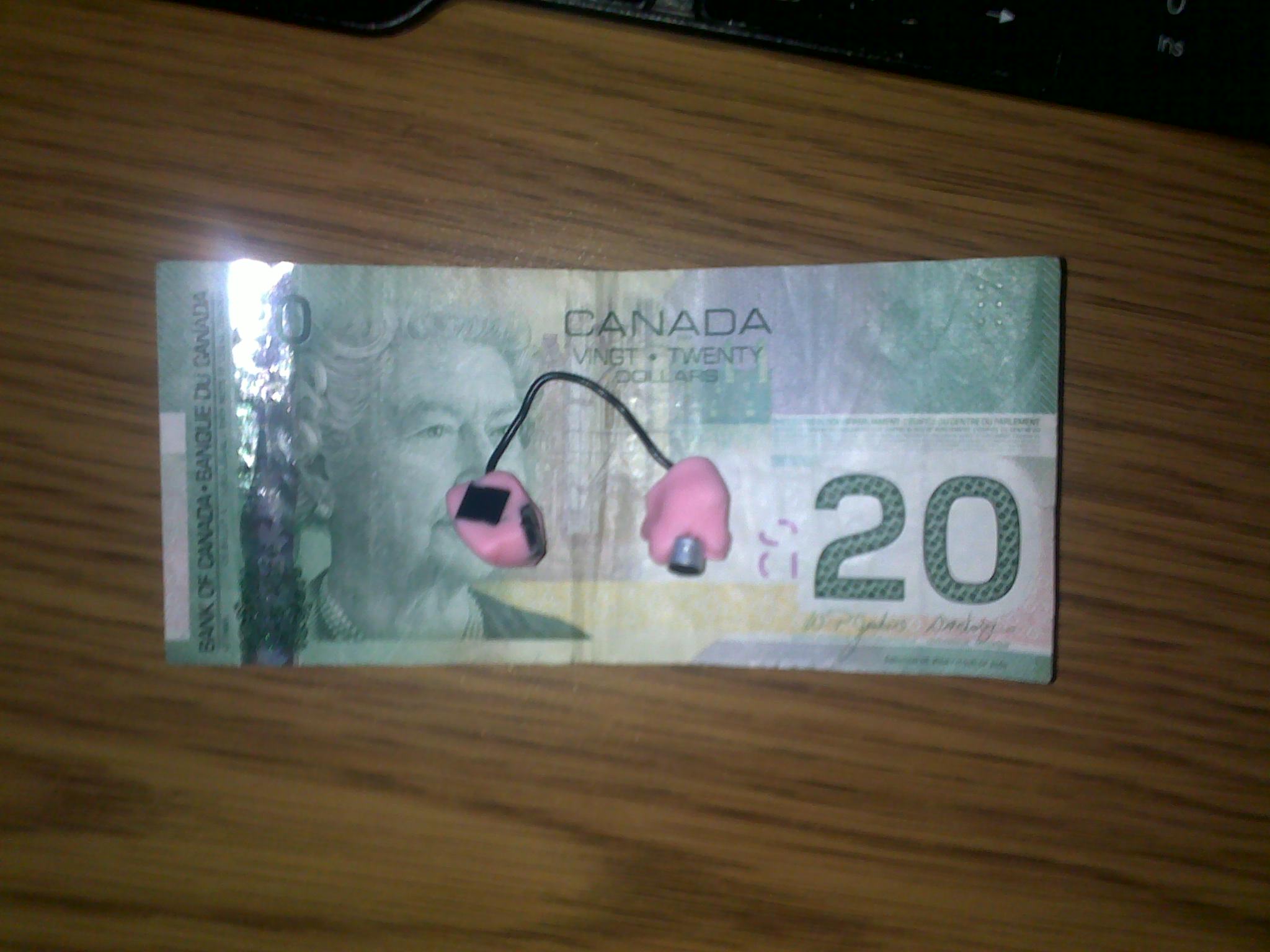
Smaller prototype.
The final result is a tiny, self-powered hearing aid (type) device with custom fitted moulds. The small speaker goes into the ear, and the portion on the left goes over and behind the ear. I even added a small push button that would make the device replay the most recent ten seconds of audio on a loop until the button was released. It was intended as a way for someone to “re-hear” something without having to ask the speaker to repeat it. Neat.
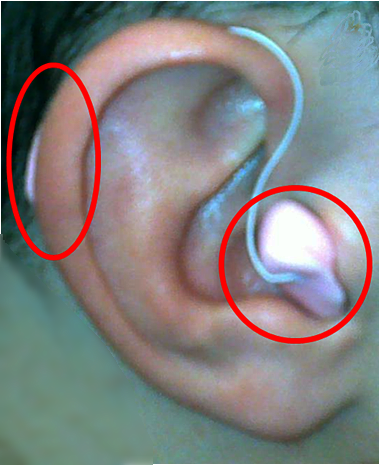
A better hearing aid, still under $10.